LDT Compliance: Countdown to May 2025
December 03, 2024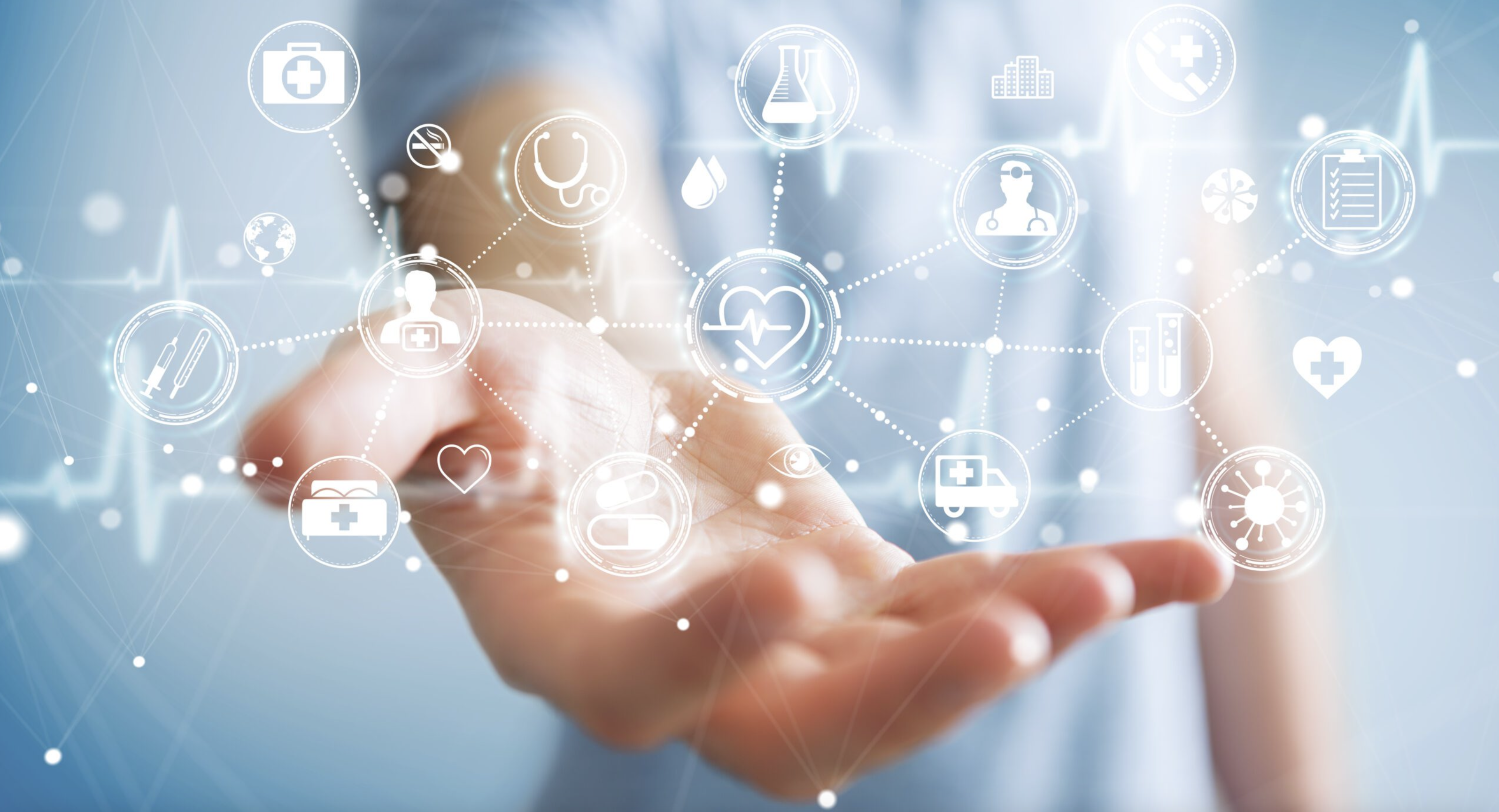
We previously reported on the FDA’s laboratory-developed test (LDT) rule published on May 6, 2024, which classifies LDTs as medical devices under the Federal Food, Drug, and Cosmetic Act (FD&C Act). This shift marks the end of FDA’s historical enforcement discretion for LDTs, transitioning to a standardized regulatory framework for in vitro diagnostics (IVDs), regardless of their place of manufacture.
To ease the transition, the FDA is phasing out enforcement discretion over four years, giving laboratories time to align with the new requirements. This phased approach aims to enhance the safety, reliability, and consistency of LDTs while ensuring patients continue to have access to critical tests for care.
Why Act Now?
Although discussions about the potential impact of a new administration and DHHS and FDA leadership may raise questions about the future of this rule, there has been no indication of changes or delays. With the Stage 1 compliance deadline looming in just five months, LDT makers should take proactive steps to prepare rather than wait for potential changes. Timely preparation is key to managing these changes, as achieving FDA compliance involves substantial planning and effort.
Stage 1 Compliance Requirements
Starting May 6, 2025, the FDA will require LDT manufacturers to comply with the following regulations as part of Stage 1 of its phased implementation:
- Complaint Files (21 CFR 820.198)
- Medical Device Reporting (MDR) (21 CFR Part 803)
- Correction and Removal Reporting (21 CFR Part 806)
Below are the key requirements and what you need to have in place for each:
1. Complaint Files Requirements (21 CFR 820.198)
Manufacturers must maintain a robust system for receiving, reviewing, and evaluating complaints. Complaint records must include details such as the nature of the issue, device identification, and any follow-up actions taken. Proper handling of complaints supports quality assurance and regulatory compliance.
- What You Need to Have in Place:
- Standard operating procedures for logging, reviewing, and categorizing complaints.
- A system for tracking all complaints, ensuring they are assigned, investigated, and resolved appropriately.
- A method to determine whether a complaint triggers MDR reporting or other regulatory actions.
- Guidelines for root cause analysis, corrective actions, and preventive measures.
- Ensure staff are trained and understand complaint intake and escalation protocols.
- Maintain records of each complaint, including device identification, investigation findings, and actions taken.
2. Medical Device Reporting (MDR) (21 CFR Part 803)
LDT manufacturers must report certain adverse events and device-related malfunctions to the FDA. This includes incidents where a device may have caused or contributed to a death or serious injury, or if the malfunction could lead to such outcomes if it were to recur. Timely reporting is required.
- What You Need to Have in Place:
- A system for capturing and evaluating adverse events and device malfunctions reported by users, patients, or healthcare providers.
- A clear process for determining whether an incident meets the criteria for reporting under MDR regulations.
- Ensure compliance with the 5- or 30-day reporting deadlines, as applicable.
- Train employees, especially those in customer service, quality, and post-market surveillance, to recognize and escalate potential MDR events.
- Maintain detailed records of all MDR submissions and justifications for non-reportable events.
3. Correction and Removal Reporting (21 CFR Part 806)
Manufacturers are required to notify the FDA of any corrective or removal actions taken to address device issues that present a risk to health or to comply with FDA regulations. Certain exceptions apply, but recordkeeping and documentation of such actions are mandatory, even if reporting is not required. We previously reported on the importance of FDA compliance when conducting a recall. Handling a recall is a time-sensitive and complex process that requires thorough preparation. Addressing it without a well-planned approach can lead to unnecessary delays and complications.
- What You Need to Have in Place:
- A framework to assess whether an issue warrants a correction or removal and requires FDA reporting.
- Written procedures for initiating, managing, and documenting corrective or removal actions.
- Tools and protocols to notify the FDA, customers, and other stakeholders about corrective or removal actions.
- If an action does not require reporting, maintain documentation explaining why reporting was unnecessary.
- Track all corrective and removal actions, including the root cause analysis, action plans, and outcomes.
Why Compliance Matters
Failure to comply with these FDA requirements can result in severe consequences, including enforcement actions, product recalls, and reputational damage. By acting now, LDT manufacturers can establish the necessary systems, policies, and training programs to meet the upcoming May 2025 deadline and avoid potential business disruptions.
Contact Us
At Gardner Law, we understand the complexities of FDA regulations and LDT manufacturers' unique challenges. Our attorneys provide tailored guidance to help you design and implement compliant systems, policies, and documentation. Contact Gardner Law to ensure your LDT operations are ready for the regulatory changes.